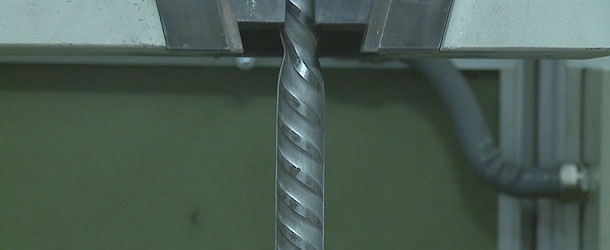
Mechanical tests
Tensile test
The test, performed at room temperature or, more rarely, at higher or lower temperatures, consists of subjecting a specimen to breakage by means of a tensile stress generated by a mechanical or hydraulic test machine.
The characteristics of the specimens and the test procedures are described in detail by the standard EN ISO 6892-1:2009.
The table reports only the variables of significant interest for the Rodacciai products. The specimen is obtained by machining of a sample taken from the product, although bars and fine wires up to a certain diameter can be tested without machining. The specimen therefore generally has a circular cross section, but in the case of hexagonal or square profiles, it can also have a cross-section of this type.
The proportional specimens have an initial length L0 proportional to the initial cross-section S0:
L0 = 5.65 S0
For diameters less than 4 mm (L0 < 4 mm), non-proportional specimens with a length of 100 mm are used, independently of the area of the initial section.
The following mechanical characteristics can be determined with the tensile test:
Variable | Symbol | Unit of measurement | Description |
Tensile strength | Rm | MPa (N/mm2) | Also called “ultimate strength”, this is the ratio between the maximum force applied by the machine and the initial cross-section of the specimen. |
Yield strength | Rs | MPa (N/mm2) | Detectable only when the material exhibits the phenomenon of yield (does not exist in draw or stainless steels). |
Specific characteristic proof stress | Rp | MPa (N/mm2) | Detectable on drawn steels and stainless steels, replacing Rs. It is the load that corresponds to a non-proportional extension equal to a prescribed percentage of the length L0. |
Rp(0,2) | MPa (N/mm2) | Load that corresponds to a non-proportional extension equal to a percentage of 0.2% of the length L0. | |
Rp(1,0) | MPa (N/mm2) | Load that corresponds to a non-proportional extension equal to a percentage of 1.0% of the length L0. | |
Percent elongation after fracture | A | % | Permanent elongation of the length L0, expressed as a percentage of the length L0. |
A5 | % | Permanent elongation for proportional specimens with a length L0 equal to 5 times the diameter. | |
A4 | % | Permanent elongation for proportional specimens with a length L0 equal to 4 times the diameter. | |
A0 | % | Permanent elongation for non-proportional specimens with a length L0 equal to 100 mm (used for diameters less than 4 mm). | |
Percent reduction of area coefficient | Z | % | Ratio between the maximum variation of the area of the cross section and the area of the initial section S0, expressed as a percent. |
Hardness test
Hardness can be defined as the resistance of the material to the penetration of a body.
The hardness tests differ in the shape of the penetrator, the loads applied and the measurement procedures: details are described in the relative standards.
Hardness tests are carried out on a flat surface of the specimen, following appropriate preparation of the surface, which should be performed more carefully the smaller the applied loads are. The impressions must have a minimum distance from the edge of the specimens and between each other.
Further information on the tests shown in the table, as well as the conversion tables between the hardness values obtained with the different systems are available in the .pdf that can be downloaded at the bottom of the page.
Hardness test and reference standard | Symbol and examples | Description |
Brinell UNI EN ISO 6506-1 | HB | An indenter (spherical steel or carbide bead) is pressed on the specimen’s surface under a given load and the diameter of the impression left after having removed the load is measured. |
HB 10/300 | Brinell hardness measured with a sphere that is 10 mm in diameter and with a load of 29.42 kN (equal to 3000 kgf) | |
HB 2,5/187,5 | Brinell hardness measured with a sphere that is 2.5 mm in diameter and with a load of 1.839 kN (equal to 187.5 kgf) | |
Vickers UNI EN ISO 6507-1:99 | HV | A pyramidal diamond indenter (with a square base and with an angle at the vertex of 136°) is pressed on the specimen’s surface under a given load and the diagonal of the impression left after having removed the load is measured. |
HV 30 | Vickers hardness measured with a load of 294.3 N (equal to 30 kgf). | |
HV 1 | Vickers hardness measured with a load of 9.81 N (equal to 1 kgf). | |
HV 0,1 | Vickers hardness measured with a load of 0.98 N (equal to 0.1 kgf). | |
Rockwell UNI EN ISO 6508-1:99 | HR | An indenter is pressed in two stages (120° diamond cone or steel sphere with a diameter of 1.5875 mm) on the specimen's surface under a determined load, and the difference in depth under the pre-load is measured between before and after the application of the load. |
HRC | Rockwell hardness carried out with a diamond cone and overall load of 1471 N (150 kgf). Valid from 20 to 70 HRC. | |
HRB | Rockwell hardness carried out with a diamond cone and overall load of 980.7 N (100 kgf). Valid from 20 to 100 HRB. | |
HRA | Rockwell hardness carried out with a diamond cone and overall load of 588.4 N (60 kgf). Valid from 20 to 88 HRC. |
Toughness test
Toughness is the capacity of a material to resist shocks.
The test consists of breaking a carved specimen resting on two supports with one fell swoop, using a pendular hammer.
The battering hammer is equipped with a knife with standardized geometry (those most frequently used are in accordance with the EN European standard and the ASTM American standard) capable of generating an energy generally equal to 300 J.
The tests are carried out at ambient temperature or, often, at a lower temperature to check if the material is subject to brittleness under those conditions.
The test result is expressed as the energy absorbed (expressed in Joules) in the collision to fracture the specimen.
Further information on the tests shown in the table, as well as the conversion tables between the toughness values obtained with the different systems are available in the .pdf that can be downloaded at the bottom of the page.
Abbreviation | Name | Length | Thickness | Height | Height of uncut section | Nominal and test section (cm2) | Cut root radius | Carving angle |
KV | Charpy V | 55 | 10 | 10 | 8 | 0,8 | 0,25 | 45 |
KCU | Charpy U | 55 | 10 | 10 | 5 | 0,5 | 1 | - |
IZOD | Izod V | 75 (1 carving) 100 (2 carvings) 130 (3 carvings) | 10 | 10 | 8 | 0,8 | 0,25 | 45 |
Mesnager | 55 | 10 | 10 | 8 | 0,8 | 1 | - |
DOWNLOAD Mechanical tests
-
Mechanical tests
Tensile test, Hardness test, Toughness test